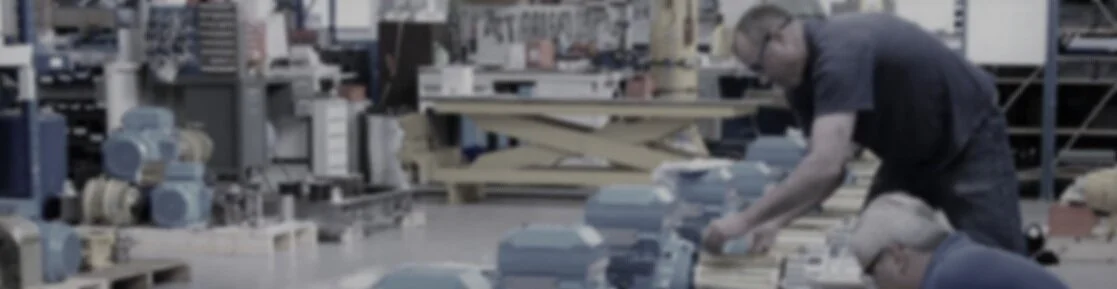
HMD Sealless Pumps Transforms its Engineering & Product Creation Process
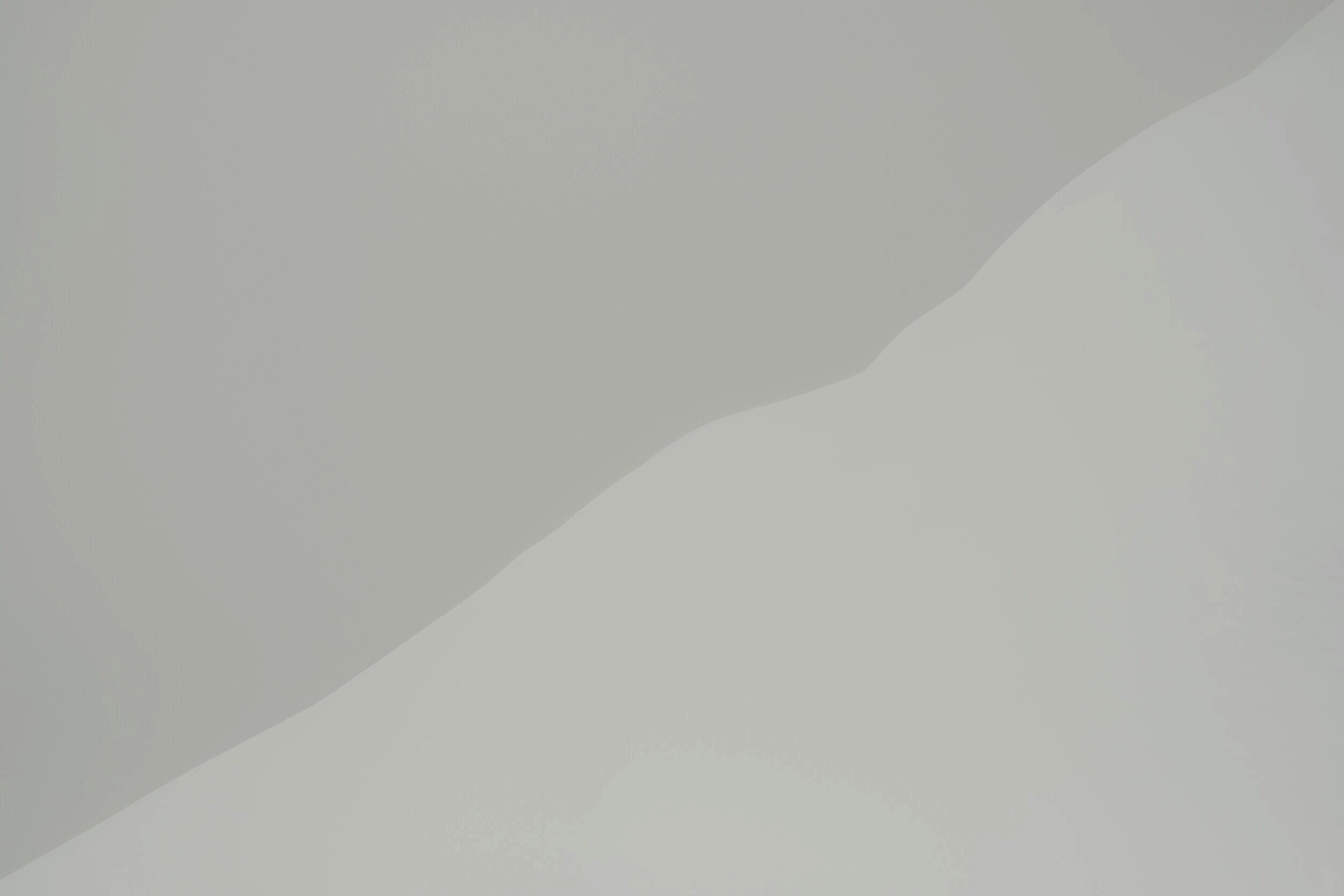
When it needed to restart its Teamcenter PLM initiative HMD turned to AESSiS to help it develop and implement a new product creation strategy.
About HMD
HMD Pumps are based on the south coast of England and pioneered the sealless magnetic drive pump over sixty years ago. The HMD sealless design brings a wide range of operational benefits because there’s no risk of harmful emissions or leaks and, with no seals to replace, they are easier to maintain and more reliable than conventional pumps.
Today, HMD produces a wide range of standard and highly engineered pumps to order. The engineered pumps create special challenges.
“Because our continued success relies on rapidly engineering pumps to order for very demanding industrial applications, we need effective PLM processes that ensure our products meet customer’s precise technical requirements whilst allowing us to minimise our engineering costs by reusing designs across projects,” says McKee.
“To grow our business we have to be able to quickly deliver new and replacement pumps at outstanding levels of quality to our customers so we recognise the importance of having world class engineering tools”
An important goal here says McKee “was keeping the Teamcenter data model as simple as possible. We knew some configuration would be necessary but we wanted to avoid over customising Teamcenter. We wanted to get the balance right and AESSiS were able to help us make sensible and pragmatic choices”.
Re-implementing Teamcenter
The journey began back in 2008. As part of a strategic review, HMD looked at their processes throughout the product lifecycle and targeted areas for improvement. The perception of PLM within HMD had been damaged because a previous implementation of Teamcenter had not gone well. Teamcenter had not been aligned with the process needs of the company and, as a result, had gradually fallen out of regular use. However, HMD is a company that is committed to continuous improvement and David Clark, the Senior Engineering Manager at HMD, recognised that an opportunity to re-energize the PLM initiative and use Teamcenter more effectively was being missed. Clark determined that what HMD needed was a fresh look at Teamcenter as a platform for achieving HMD’s goals.
HMD decided to work with AESSiS to help deliver the new approach. According to McKee, “After the disappointment of the initial Teamcenter roll out, it was critical to HMD to get an expert and independent perspective and we were quickly impressed by AESSiS’s ability to provide clear, refreshing and objective input. AESSiS were also able to deliver a very proactive and solution based approach, and at a more competitive price than we had experienced before, which resulted in a much better ROI for us”.
The new initiative began with a PLM ‘diagnostic’ exercise to measure how current engineering processes compared to PLM best practice and to establish consensus and a clear vision of how HMD’s future processes should work in the context of Teamcenter.
AESSiS and HMD then worked together to map the company’s requirements onto the Teamcenter tool set.
Central to this effort was defining how HMD should structure its engineering bill of materials in Teamcenter. McKee again; “HMD build a tremendous number of pump products and product derivatives. Many of these, at first glance, appear geometrically very similar. They are differentiated however by the specification of a wide range of advanced materials which are absolutely crucial for performance in the demanding applications that our pumps are used. We needed an approach to model this complexity whilst providing an easy way to reuse design information across our pump range”.
The solution that the team came up with was a highly visual product structure framework, underpinned by a new Teamcenter data model.
This new framework allowed HMD designers and engineers to work together concurrently to model both the ‘as-designed’ and ‘as-built’complexities of their pump range and to easily find and reuse designs between projects and products. It also made significant use of advanced CAD modelling techniques particularly WAVE. With this framework, engineers were able to use Teamcenter’s product visualisation capabilities with confidence to visualise complete pump packages and identify engineering issues much earlier in the project lifecycle.
By early 2010, HMD were ready to embark on the next leg of the journey and extend Teamcenter into Manufacturing by including Parts, Operations & Routings in the data model.
An important feature of HMD pump designs is that the same geometric design may be manufactured using different materials depending on the substance being pumped. But of course it’s not efficient to maintain lots of separate CAD models and assemblies when the only difference is a material specification on a drawing.
The answer was to create a Teamcenter ‘Part’ item type to reflect the product as manufactured and against which could be defined part specific information such as the number, name, material and testing specifications (to name but a few). ‘Design’ items could then be attached to these parts (and indeed reused across lots of different parts).
In addition, a custom ‘Operation’ item type was created to define all the operations required to make the part and a ‘Routing’ item type was added to organise the operations according to how the product was built on the shop floor. Operations and Routings were then attached to the ‘Parts’ alongside the ‘Design’ to fully specify how parts are designed and built.
Another key goal was to reduce manual data entry and re-entry into HMD’s manufacturing systems so the final step was to create a tool to export all this information into a neutral file that could be automatically read into the MRP system as part of the release process. Thus when the new pump was released in Teamcenter, Part, BOM & Routing information would automatically appear in MRP.
2011-12 A Big Teamcenter Upgrade
When Teamcenter was first implemented at HMD, before the arrival of AESSiS, it was done so on Teamcenter version 2005 using an Oracle database. But all HMD’s other business systems are standardised on MS SQL so HMD were carrying the cost of maintaining both databases. This made no sense. In addition, a large amount of legacy data had been migrated into Teamcenter during the first implementation. But this had turned into a hindrance because it was occupying item numbers that the team wanted to use elsewhere. A decision was therefore taken to do a complex migration of data to Teamcenter version 8.3 (Unified) running on MS SQL 2008 R2. This posed a number of challenges.
The migration had to;
• Skip several intermediate versions of Teamcenter.
• Move data from Oracle to MS SQL
• Selectively migrate only data attached to HMD’s new data model leaving behind the old legacy data.
• Support a CAD tool change from NX5 to NX7.5
• Preserve all WAVE links maintained in Teamcenter and transfer them intact to Teamcenter version 8.3.
The AESSiS team began by building a completely new Teamcenter 8.3 environment on MS SQL on new server hardware.
The HMD data model was then transferred in Teamcenter 8.3 and custom tools were developed and implemented to extract the target data from the old Teamcenter environment before importing it into the new Teamcenter 8.3 environment. The actual migration was then carried out successfully in several chunks allowing the design team to go live in the new system with a minimum of disruption.
2013/2014 HMD Gets a New Owner
In 2013, Sundyne the parent company of HMD, was acquired by Accudyne Industries which is a leading global provider of advanced flow control systems.
Previously all server hardware was provided by CSC but with the acquisition this changed to a new provider and HMD were obliged to acquire all new server & client hardware. AESSiS were again on hand to rebuild Teamcenter on the new hardware and, at the same the opportunity was taken to roll-out Teamcenter Web for the users outside design and deploy NX8.5 for the designers.
In 2014, with the systems side settling down at last, the emphasis returned to expanding the scope of the Teamcenter deployment. Computer-aided Engineering With ‘engineering to order’ being a big part of the HMD business, accurate simulation can reduce costs & product lead-times significantly and therefore plays a important role in the product development process. The team has deployed a new CAE data model in Teamcenter to manage the CAE data effectively alongside the design data to further improve information reuse.
Computer-aided Manufacturing
HMD invest heavily in the latest machine tools so having an effective and efficient interface to their numerical control (NC) programming tool is hugely important. The Teamcenter data model is being expanded further to allow HMD’s Delcam application to access and save files to and from Teamcenter in a robust manner.
Supplier & Partner Data Exchange
HMD work with a variety of design partners and some of these do complex design work. Until now HMD have been exchanging data at the file level via email and FTP. But when you are working with complex assemblies, this is error prone and inefficient. The team is implementing a more sophisticated approach via the cloud. Full assemblies will be sent to partners so that they can work on a component in the context of the assembly. Changes are then automatically merged back into the HMD design with any modified components given a new item revision. Full traceability will be provided at the same time.
Quality Management
Quality processes are being brought into the scope of Teamcenter for the first time. Starting with the Non Conformance process, bringing quality procedures into Teamcenter will help ensure that the quality organisation is more closely connected to and kept abreast of rapidly changing set of product information and quality related processes and information will be more closely integrated into the broader flow of engineering information.
Conclusions
Ultimately, the Teamcenter implementation at HMD is all about providing HMD customers with the very high quality product they have come to expect more cost effectively and at lead times that better the industry expectation. It has not always been an easy journey but Teamcenter has staked its claim at HMD and is doing a good job. And of course, the journey continues. The key to its success so far has been a great team effort between HMD’s Engineering and IT teams and AESSiS. And with this team in place, Teamcenter will continue to deliver the value that the HMD business needs long into the future.